In STREAMS, AETC will beneficiate the graphite from the Chilalo project as well as from recycled black mass, and will also prepare Si/C composites, delivering all these components and intermediates to the STREAMS consortium (Work Package 2 and 5).
Meet the faces behind the project
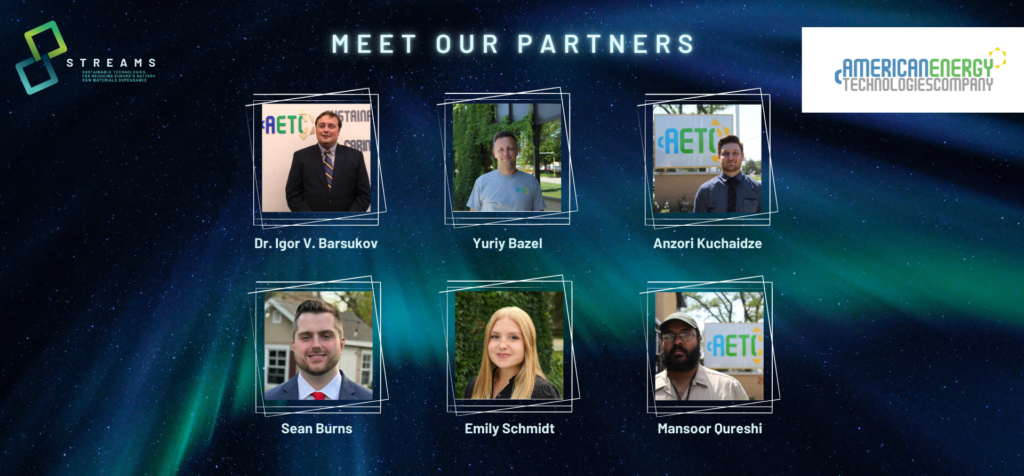
Dr. Igor V. Barsukov, an Executive MBA with the University of Illinois and an Honorary Professor KNUTD, is AETC’s Manager, Business Development as well as a company officer. Dr. Barsukov is a professional materials scientist and electrochemist. He is well known for his work with carbons and batteries. Within 1998-2009, Dr. Barsukov has developed and commercialized several grades of carbon, which presently directly benefit the US and International battery market, including Alkaline, Lead Acid, Lithium-Ion and Li primary batteries. New materials, developed under Dr. Barsukov’s efforts complemented critical technological advancements in the following well-known consumer battery platforms: “Energizer® New Advanced Formula®”, “Energizer® e2”, “Rayovac Maximum PlusTM”, “Cegasa Super Alkaline”, “Rayovac Infinity Gold®”, Varta® High Energy, etc. As of 2009 he and the rest of AETC team have put on the market 4 new graphites and 3 fully developed unique long calendar life Lithium primary battery systems for specialty applications. For AETC tasks relevant to project STREAMS Dr. Barsukov organizes and tracks work by task, sets priorities, and manages the submission of deliverables to the Consortium.
In STREAMS, Dr. Igor Barsukov manages the engineering, startup and operation of an innovative battery recycling technology, known as AETC’s Direct Recycling Technology. In accordance with AETC’s approach, spent lithium-ion battery cells are carefully disassembled, followed by mechanical separation, to produce “cleaned” black mass. AETC operates an innovative process of recycling that retrieves battery components (cathode, anode and separator) as separate streams. The “repair” or “healing” of the graphite anode is be done post-anode-recovery. The main steps in this process are the classification of the recovered mass, sizing, purification, re-spheroidization, classification, and re-carbon-coating. Before the final step, some additives will be composited with the healed material to build a performance-enhanced anode. This activity will contribute to D5.1.
Also, a team led by Dr. Igor Barsukov will closely work with Consortium members BUL, Enviva and UNE on tasks related to Eco-design requirements and regulatory framework, Environmental and social Impact Assessment, Techno-economic evaluation, Harmonized Life Cycle Sustainability Assessment and circularity assessment, as well as on the in-depth engineering design of a high-temperature furnace for synthesis of purified and graphitized forms of anode-grade carbon that was either recovered from spent batteries or derived from secondary sources of carbon and the Design of a pilot plant, including production line planning, which will integrate promising technologies developed in this project and benefiting from the battery-ready anode manufacturing technologies. This activity will contribute to D7.1, D7.2, D7.3, D7.5, D8.4 and D8.5.
“Greetings from American Energy Technologies Co. (AETC), a Chicagoland’s innovative processor of battery-ready industrial graphite and carbon! We are a private, closely held woman-owned small business concern which operates in the US and international markets. AETC is currently the only industrial manufacturer in the US of spherical purified surface coated graphite, a component which makes up 48% of the bill of materials (BoM) of advanced lithium-ion batteries for use in electric vehicles, stationary power energy storage (supporting solar and wind power stations), and specialty applications. Besides its production branch, AETC is known worldwide for its cutting-edge engineering services related to pre-feasibility and bankable feasibility level qualification of natural and synthetic graphite precursors from around the world. AETC has been known to provide rigorous testing and capabilities for upgrading graphite before it becomes battery-ready material. AETC is also recognized within the industry as the go-to organization for qualifying feedstocks and rendering them suitable or non-suitable for use in advanced battery markets. As part of streams we have launched a revolutionary Direct Recycling Technology which is agnostic to the battery chemistry employed in the cathode and is characterized by its robustness, simplicity, sustainability and low cost over traditional processing methods. Stay tuned to witness how this technology will benefit STREAMS project. We are very excited to work with you!”
Yuriy Bazel is Electrical and Control Engineer with over twenty years of experience in energy systems and process automation. He has dedicated significant effort to optimizing and accelerating the processes of discharging and disassembling battery cells. His work ensures the efficient reuse of materials in the manufacture of new batteries and the proper disposal of unusable materials.
“Just do it, create, try, experiment, never give up and then you will succeed.”
Anzori Kuchaidze is the Leading Mechanical Engineer at AETC, specialising in Process and Industrial Engineering, plant design, and scale-up. He creates detailed process flow diagrams, which form the foundation for large-scale automated solutions for AETC’s clientele. He also develops and models 3D solutions for internal prototyping and external manufacturing. In the STREAMS project, Anzori focuses on the Research and Development of battery disassembly processes, including manual, semi-automated, and fully automated component separation. Additionally, he works on the downstream preparation of cathode materials for subsequent processing by STREAMS partners in Europe.
“Should man leave a monument, let it be greenest lands and the bluest oceans.”
Sean Burns Mechanical Engineer at AETC, specialising in the development and modeling of solutions for both internal prototyping and external manufacturing, as well as process development and quality control testing. He assists in creating industrial process flow diagrams, which serve as the foundation for large-scale automated solutions for AETC’s industry partners. Within the STREAMS project, Sean focuses on the Research and Development of battery disassembly processes, including manual, semi-automated, and fully automated component separation. He is also involved in preparing anode materials for downstream beneficiation through AETC’s “Inverted Flowsheet” technology, which produces battery-ready anode-grade graphite.
Emily Schmidt serves as the Business Development Representative and Project Manager at AETC. In her role as the project manager for STREAMS, she facilitates communication between AETC and the other organizations involved in the project. She organizes and presents data generated by the AETC team during the recycling and processing of batteries, creating cohesive presentations for WP and Plenary Meetings. Additionally, Emily assists in the development of a life cycle assessment for AETC.
“I’m so glad I get to play a role in this innovative STREAMS project and work with all the highly reputable organizations on the STREAMS Consortium. We are the only people in this project working on a direct-recycling approach of Li-ion batteries and I am very excited to see the end results, especially the increase in efficiency, the domestic supply aspect and circularity of electric vehicles. This really is a revolutionary project that will have a beneficial effect on our environment and will demonstrate supply chain safety for EV batteries.”
Mansoor Qureshi is Industrial Chemist who plays a crucial role in the recycling of batteries at AETC. He is responsible for much of the groundwork in preparing materials that are further processed into anodes, cathodes, and separators by various partners in the STREAMS Consortium.
About AETC
American Energy Technologies Company (AETC) is a woman-owned, privately held business concern which conducts operations out of the greater Chicago area, Illinois, USA. In its Arlington Heights, IL facility AETC operates three business units: a manufacturing plant producing battery-ready graphites and carbons, a pilot demonstration facility for battery materials and graphite dispersions, and a fully-functional research and development laboratory supporting the above business units. AETC is responsible for preparing black mass from NMC and LFP cells.
Follow AETC: